Inspection and Testing
Inspection and Testing are integral components of Venus’s commitment to delivering the highest quality stainless steel products to our valued clients. We adhere to a stringent testing system that encompasses a comprehensive range of assessments, ensuring that our products meet and surpass industry standards. These tests, conducted both during the in-process and final inspection stages, are broadly categorized into two distinct groups.
The first category involves physical tests, where the structural integrity and mechanical properties of our stainless steel pipes and tubes are meticulously examined. These tests include dimensional checks, tensile strength evaluations, hardness assessments, and elongation tests. By subjecting our products to these rigorous physical examinations, we can guarantee their durability, reliability, and suitability for a wide range of applications.
In the second category, we focus on non-destructive testing techniques to detect any hidden flaws or imperfections. This involves ultrasonic and radiographic examinations, which allow us to inspect the internal structure of our products without causing any damage. Additionally, dye penetrant tests are employed to identify surface defects that might compromise the integrity of the stainless steel. By combining physical and non-destructive testing methodologies, Venus ensures that every product leaving our facilities is of the highest quality, meeting the exacting standards of our discerning clients.
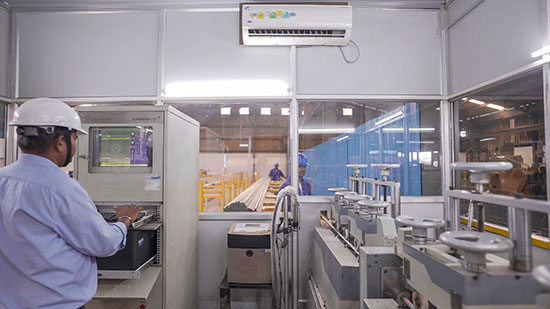
Destructive Tests
- Tensile Test
- Hardness Test
- Hardness Test
- Flaring Test
- Flange Test
- Reverse-bend Test
- Reverse Flattening Test
- Impact Test
- IGC Test – Practive A, B, C & E
Non Destructive Tests
- Hydro-static Test
- Eddy Current Test
- Ultrasonic testing
- Air Under Water Test
- P.M.I. Test
- Spectro Test
- Dye Penetrant Test
- Borescope Test